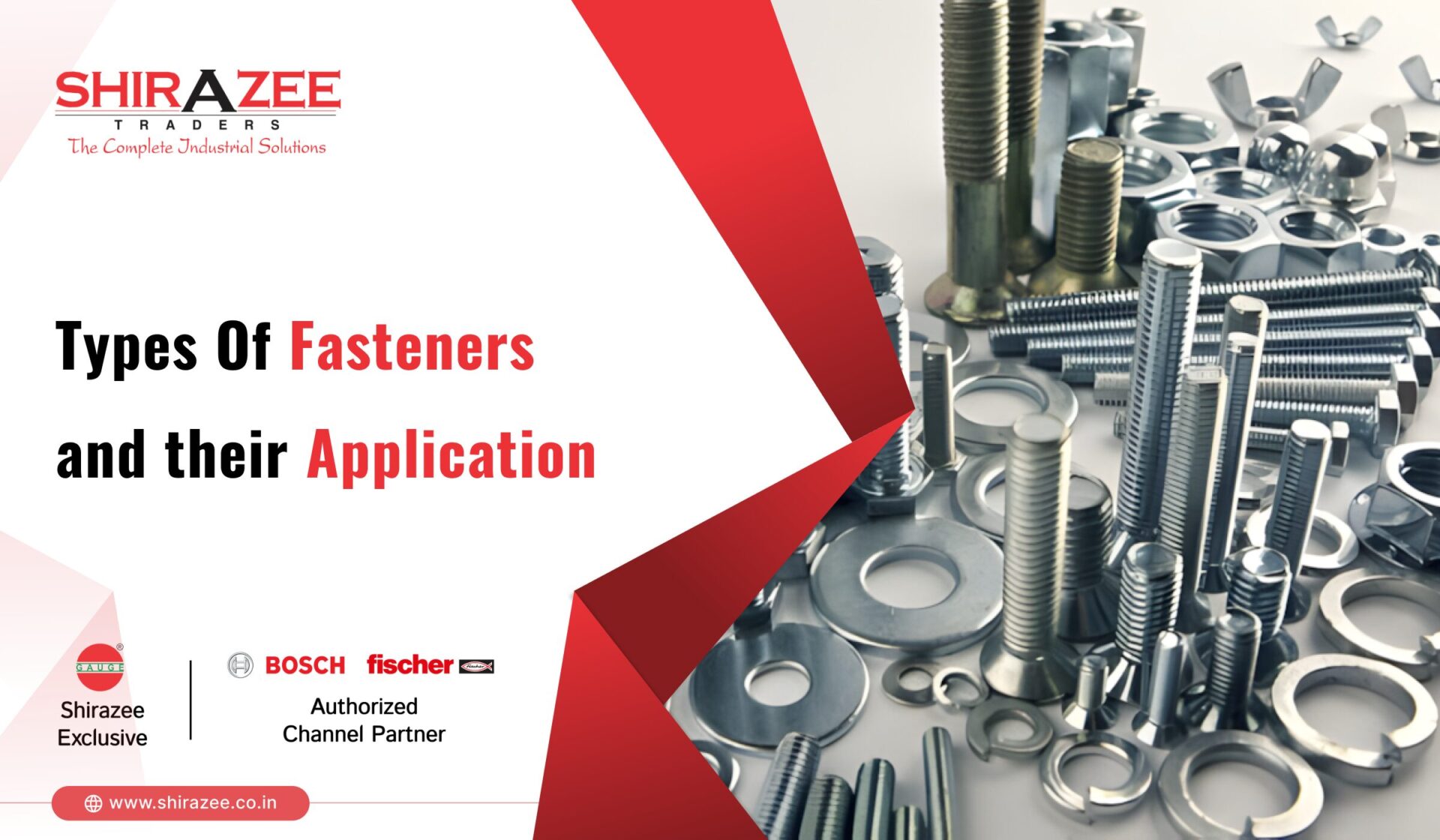
Fasteners play an essential role in a myriad of sectors, acting as key components in fields such as construction, manufacturing, the automotive and aerospace industries, and electronic applications. These small but mighty tools are critical for building infrastructure, assembling machinery, and ensuring the structural integrity of various systems. This blog emphasizes the diverse types of fasteners and their specific applications. By understanding the role and function of different fasteners, professionals can make informed decisions that enhance the durability and functionality of their projects.
Types of Fasteners and Their Uses
1. Socket Screws and Machine Screws
Socket Screws and Machine Screws play a crucial role in ensuring that components fit together perfectly and operate smoothly. Socket screws, characterized by their hexagonal socket in the screw head, are typically driven with an Allen wrench, which allows for more torque to be applied with minimal slippage. This makes them ideal for applications where space is limited or where a smooth outer surface is necessary. Machine screws, on the other hand, feature a uniform thread along the entire length of the screw, making them perfect for use with tapped holes and nuts. They come in a variety of head styles, including flat, pan, round, truss, and oval, which makes them versatile for use in everything from electronic devices to large machinery. Socket screws and machine screws come in a variety of sizes and are made from different materials such as stainless steel, brass, and alloy steel. These materials are chosen based on the specific environmental conditions and strength needs they must meet.
2. Tapping Screws and Hex Bolts
Tapping screws and hex bolts are integral components in construction and manufacturing due to their distinct design and functional properties. Tapping screws are uniquely designed to create their own thread as they are driven into materials such as metal or plastic. This self-threading feature eliminates the need for pre-drilled holes, strengthening the assembly process and enhancing speed and efficiency in both temporary and permanent applications. They come in various types, including sharp-pointed and blunt-ended designs, each catering to specific material types and installation needs. Hex bolts, characterized by their six-sided hexagonal head, are widely used in heavy-duty applications. They require a nut or a tapped hole to secure components together, providing a powerful and reliable grip. These bolts are favored for their versatility and strength, making them essential in construction projects and machinery repairs. The design of hex bolts allows for easier tightening and removal with standard tools like wrenches and sockets, which is crucial in high-torque situations.
3. Hex Nuts, Weld Nuts, and Castle Nuts
These nuts are required in various applications across industries, providing a strong hold and stability in assembly. Hex nuts are the most universally utilized, recognized for their versatility and reliability in securing bolts across a wide range of mechanical and structural applications. Weld nuts are designed for a more specialized purpose, typically used to create a permanent bolted joint where they are welded into place, enhancing structural integrity. Castle nuts, distinguishable by their marked perimeter, are employed in low-torque applications; they are secured with a cotter pin through the nut and bolt, preventing movement and loosening under vibration, making them ideal for safety-critical assemblies like vehicle wheel axles and bicycle crankshafts. This combination of fasteners ensures adaptability and safety across a variety of engineering and construction projects.
4. Carriage Bolts and Eye Bolts
Carriage bolts, characterized by their smooth, rounded head and a square section underneath, are designed to fit into a square hole in wood, preventing the bolt from turning as the nut is tightened. This feature makes them ideal for wood-to-wood joining, particularly in furniture construction and deck building, where a smooth finish and safety from protruding heads are required. Eye bolts, on the other hand, feature a loop or circle at their head, which allows for attachment of ropes or cables. This design is particularly useful for lifting applications or securing cables and chains in both industrial and marine environments, providing a strong anchor point. Both types of bolts are vital in their respective roles, ensuring structural integrity and functionality in their applications.
5. Flat Washers, Spring Washers, and Ribbed Washers
Flat Washers, Spring Washers, and Ribbed Washers are crucial in various assembly processes to ensure the longevity and integrity of bolted joints. These washers help distribute the load of a threaded fastener, preventing damage to the surface being fixed. Flat washers provide spacing and load distribution, enhancing the surface area contact between the bolt head or nut and the part being secured, thus reducing pressure and preventing pull-through. Spring washers, known for their flexibility, counteract loosening through vibrations and dynamic loads by applying a constant load, which maintains bolt tension and assembly integrity. Ribbed washers offer an added advantage with their increased friction and resistance to rotation, making them suitable for preventing loosening in high-vibration environments. Each type of washer is designed to meet specific mechanical requirements and operational conditions, ensuring the reliability and safety of the assembly.
6. Blind Rivets and Semi-Tubular Rivets
Blind rivets and semi-tubular rivets are crucial where materials need to be joined securely, yet only one side of the assembly is accessible. Blind rivets are particularly valued in confined or narrow spaces where traditional riveting tools can’t reach the backside of the material. They are designed to expand within the hole to form a strong, permanent joint from one side, ensuring structural integrity. Semi-tubular rivets differ slightly, featuring a partially hollow shaft that reduces the force needed for application, which makes them ideal for softer materials or when less installation force is desired. Both types provide powerful solutions in industries ranging from automotive to aerospace, where safety and precision are valuable. These rivets are also chosen for their efficiency and reliability in assembly processes, ensuring consistent performance across varied applications.
7. Common Nails and Finishing Nails
Common nails and finishing nails are two of the most fundamental types of fasteners used extensively across various construction and carpentry projects. Common nails are strong, typically larger in size, and are employed in structural work where the visual finish is not a priority. They are characterized by their thicker shaft which provide high strength and durability, making them ideal for heavy-duty construction such as framing, sheathing, and subflooring. On the other hand, finishing nails are smaller with a smaller head, designed to be minimally visible on the surface. They are used where a neat, clean appearance is essential, such as in molding, cabinetry, and other fine woodwork. These nails are designed to disappear into the surface, which can then be filled and painted over to create a smooth, flawless finish in decorative applications.
Conclusion
Choosing the right fastener is crucial for ensuring the structural integrity and durability of assemblies in various industries. The decision involves several factors including material compatibility, environmental conditions, load requirements, and accessibility for maintenance. Stainless steel fasteners are often preferred in corrosive environments due to their rust resistance, while titanium fasteners are valued in aerospace applications for their strength-to-weight ratio. Additionally, factors like thermal expansion, electrical conductivity, and magnetic properties must also be considered to avoid material degradation, electrical issues, or interference with sensitive instrumentation. A properly selected fastener can prevent failures, reduce maintenance costs, and prolong the operational life of an assembly. This ensures that every component, whether it’s exposed to high temperatures, vibrations, or moisture, is securely and appropriately fastened, minimizing the risk of damage and failure under operational stresses.